Hydraulic-Pneumatic Devices
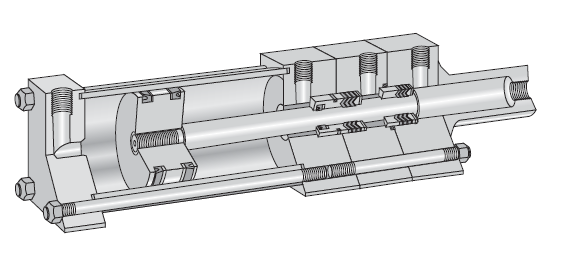
Booster
What is a booster?
A booster, or pressure intensifier, is a device that amplifies available line pressure in order to perform work requiring much higher pressure. A booster is basically a cylinder and is similar in internal design, except that the rod end of the piston does not extend outside. It changes the ratio of pressure input to pressure output. The discharge has an amplified pressure potential equal to the product of the supply pressure and the booster ratio. Boosters can save space and weight by replacing extremely large, low pressure cylinder with a small, efficient, high pressure cylinder. A booster can also lower cost because booster systems are overall less expensive with its pump-motor requirements and require a fraction of the air of a direct cylinder installation. Boosters also provide smoother power to the working cylinders.
Applications for Boosters
- High pressure from low pressure shop air
- Testing of manufactured parts for physical strength
- Fluid transfer
- Liquid injection for use of lubricants, antifreeze or odorants
- Holding pressure without drawing power or generating heat
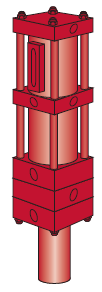
Air-Oil Tanks
Air-Oil tanks are used as a source of oil to compensate for any loss in hydraulic systems. They can provide hydraulic pressure to return the cylinder to its starting position and also provide an outlet for entrapped air in the hydraulic system
- Maximum pressure is 250 psi
- Can with stand temperatures up to 200°F (93°C)
- High strength, soil steel end caps with large fill and drain plugs for fast circuit filling
- Steel tubing sealed to each end cap with compression type gaskets
- Replaceable sigh gauge enclosed in aluminum shield for maximum gauge protection
- A unique baffle system, inside both end caps, assures rapid intake and discharge with a minimum of churning, foaming and aeration.
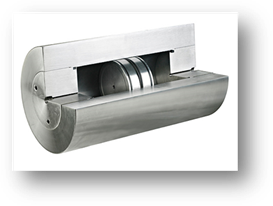
NA Series Accumulators
NA accumulators can be applied to:
- Simplify hydraulic circuit design
- Lower the hydraulic cylinder horsepower requirements
- Performing extremely fast cylinder cycle operation while in motion
- Cushioning peak loads
- Shock absorbtion
- Compensating for circuit leakage
- Maintaining constant loading on holding circuits
- Reducing pump size and circuit horsepower
- A safety device – in case of pump failure – hydraulic power is available to activate brakes or other locking devices